Oil-immersed transformers are crucial components in electrical power distribution, but understanding their internal workings can be complex. If improperly maintained or designed, these transformers can suffer from overheating, insulation breakdown, and efficiency losses—leading to costly failures and power outages. However, by understanding how the core, windings, and insulating oil interact, engineers and operators can optimize performance, ensure reliability, and extend service life.
Oil-immersed transformers function through the combined action of three critical components: the core, which channels magnetic flux; the windings, which conduct electrical energy; and the insulating oil, which cools and protects the system. The core reduces energy losses by providing a low-reluctance path for magnetic fields, the windings enable voltage transformation, and the oil dissipates heat while preventing electrical breakdowns. These elements work together to ensure efficient and safe electrical power conversion.
A deeper understanding of these three elements and their interdependence is essential for improving transformer reliability and efficiency. Let’s explore each component in detail.
What Is the Role of the Core in an Oil-Immersed Transformer?
Oil-immersed transformers play a critical role in electrical power distribution, and at the heart of their operation is the transformer core. A poorly designed or malfunctioning core can lead to excessive energy losses, overheating, and reduced efficiency. Understanding the function of the core is essential for optimizing transformer performance and longevity.
The transformer core serves as the magnetic circuit that facilitates the efficient transfer of electrical energy between the primary and secondary windings. It minimizes energy losses by providing a low-reluctance path for the magnetic flux, enhancing efficiency and stability in power distribution systems.
To fully grasp the significance of the transformer core, we need to explore its design, materials, loss mechanisms, and operational implications. This article will provide an in-depth analysis of the core’s role, ensuring that engineers, manufacturers, and maintenance professionals can make informed decisions regarding transformer design and maintenance.
The core of an oil-immersed transformer only provides mechanical support.False
The core primarily facilitates magnetic flux transfer, reducing energy losses and ensuring efficient power conversion.
1. Function of the Core in an Oil-Immersed Transformer
The core in an oil-immersed transformer is crucial for efficient electromagnetic energy conversion. It performs multiple roles:
- Magnetic Flux Conduction: The core forms a closed-loop path that channels the magnetic field generated by the primary winding, enabling electromagnetic induction in the secondary winding.
- Minimization of Magnetic Reluctance: The core’s material (typically laminated silicon steel) is designed to offer minimal opposition (reluctance) to the flow of magnetic flux.
- Reduction of Core Losses: The laminated structure minimizes eddy current losses, while high-permeability materials reduce hysteresis losses.
- Structural Support: The core also provides mechanical support for the windings, ensuring proper alignment and stability.
2. Core Materials and Their Impact on Transformer Performance
The choice of core material significantly influences transformer efficiency and performance. Below is a comparative table of common transformer core materials:
Core Material | Magnetic Permeability | Eddy Current Loss | Hysteresis Loss | Typical Application |
---|---|---|---|---|
Silicon Steel | High | Low | Moderate | Power Transformers |
Amorphous Metal | Very High | Very Low | Low | Energy-Efficient Transformers |
Ferrite | Moderate | Negligible | Low | High-Frequency Transformers |
Nickel Alloys | Very High | High | Moderate | Precision Applications |
- Silicon Steel Laminations: The most common material, known for its balance of low losses and cost-effectiveness.
- Amorphous Metal Cores: Used in energy-efficient transformers due to their exceptionally low core losses.
- Ferrites and Nickel Alloys: Applied in specialized applications such as high-frequency transformers.
3. Core Losses and Efficiency Optimization
Core losses directly impact transformer efficiency. The two primary core losses are:
A. Hysteresis Loss
Hysteresis loss occurs due to repeated magnetization and demagnetization of the core material. This energy loss manifests as heat.
B. Eddy Current Loss
Eddy currents are circulating currents induced in the core material, causing resistive heating. Laminating the core reduces eddy current losses.
Techniques to Minimize Core Losses:
- Use of Grain-Oriented Steel: Aligning grain structures reduces hysteresis loss.
- Thin Laminations: Thinner laminations reduce eddy current formation.
- Improved Cooling Methods: Oil immersion enhances heat dissipation, preventing core overheating.
4. Core Design and Magnetic Flux Distribution
Transformer core designs vary based on application requirements:
Core Type | Magnetic Path Shape | Application |
---|---|---|
Core-Type | Vertical and Horizontal | Power Distribution |
Shell-Type | Encased Windings | Industrial and High-Load Applications |
Toroidal | Circular Magnetic Path | High-Frequency and Low-Noise Applications |
- Core-Type Transformers: Suitable for large-scale power transmission due to ease of construction.
- Shell-Type Transformers: Offer superior magnetic shielding and are used in high-load applications.
- Toroidal Cores: Reduce stray magnetic fields and enhance efficiency in specialized applications.
5. Impact of Oil Immersion on Core Performance
Oil serves multiple functions in oil-immersed transformers, including:
- Cooling: Dissipates heat generated by core losses.
- Electrical Insulation: Prevents arcing between winding turns.
- Moisture Protection: Reduces oxidation and material degradation.
Proper maintenance of transformer oil ensures core longevity and efficient operation.
6. Common Issues and Solutions in Transformer Cores
Issues related to the transformer core can significantly affect performance. Below are some common problems and their solutions:
Issue | Cause | Solution |
---|---|---|
High Core Losses | Poor Material Selection | Use Low-Loss Silicon Steel |
Overheating | Inadequate Oil Circulation | Ensure Proper Cooling and Oil Filtration |
Noise and Vibration | Loose Core Laminations | Secure Core with Proper Clamping |
Core Saturation | Excessive Magnetic Flux | Optimize Core Sizing and Flux Density |
Regular testing methods such as core loss measurement, vibration analysis, and oil dielectric testing help in early fault detection.
How Do Windings Function in an Oil-Immersed Transformer?
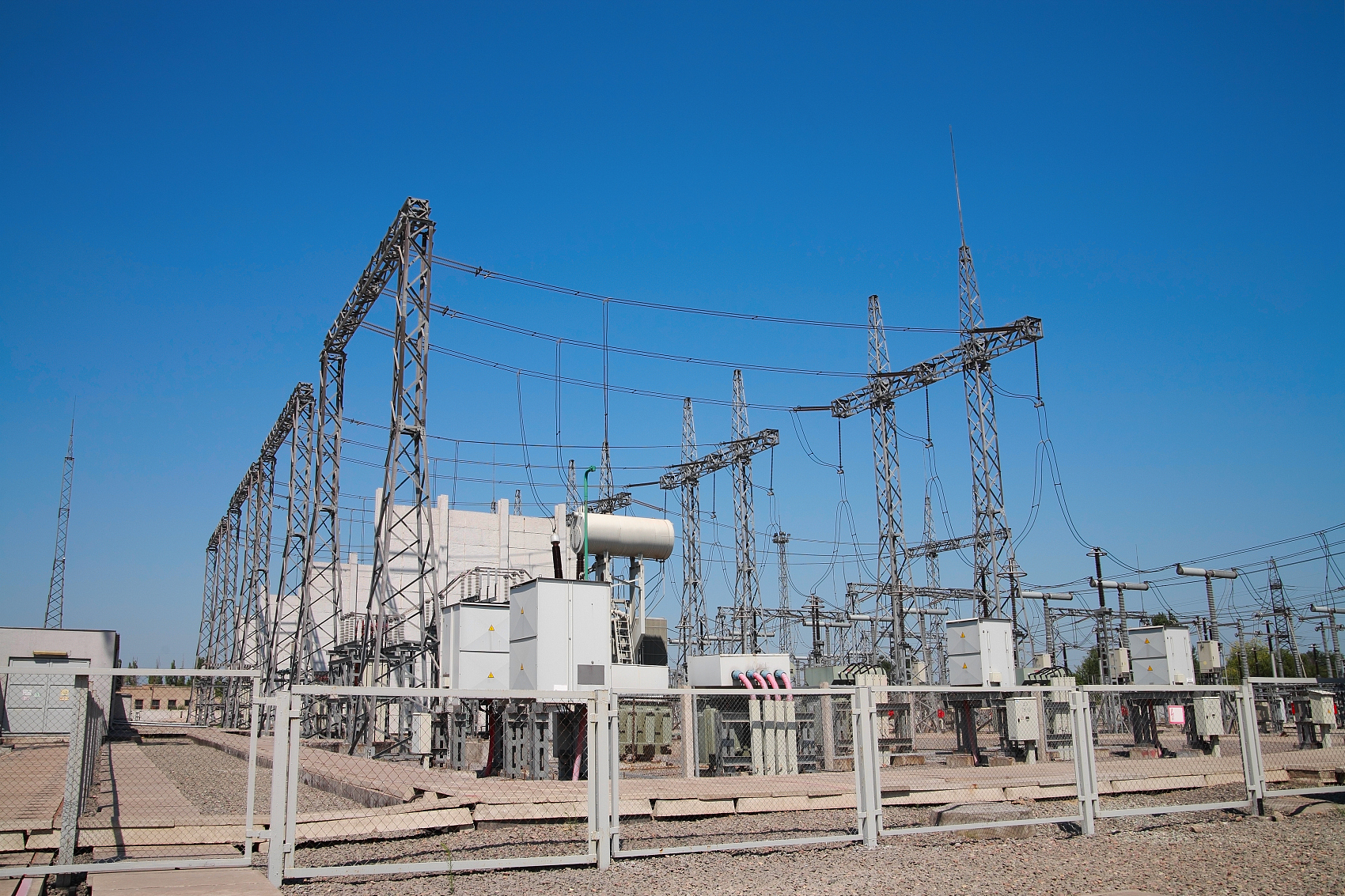
Transformers are the backbone of electrical power transmission and distribution, ensuring efficient voltage conversion. In oil-immersed transformers, windings play a crucial role in transferring electrical energy through electromagnetic induction. If the windings are poorly designed or malfunction, it can lead to inefficiencies, overheating, and catastrophic failure. Understanding how windings function is essential for engineers, manufacturers, and maintenance professionals to ensure optimal transformer performance.
Windings in an oil-immersed transformer serve as the primary and secondary conductive paths that facilitate electromagnetic induction. They convert electrical energy from one voltage level to another while minimizing power loss. The windings are insulated and immersed in oil to enhance cooling, reduce electrical stress, and improve overall transformer efficiency.
This article explores the structure, materials, types, and operational aspects of transformer windings, providing insights into their critical role in power distribution.
Transformer windings only serve as electrical conductors.False
Windings not only conduct electricity but also play a key role in electromagnetic induction, insulation, and heat dissipation.
1. Function of Windings in an Oil-Immersed Transformer
Transformer windings are responsible for voltage transformation through electromagnetic induction. Their primary functions include:
- Voltage Step-Up and Step-Down: The primary winding receives electrical energy, creating a magnetic field that induces voltage in the secondary winding.
- Current Regulation: Windings determine the current capacity of the transformer based on their wire gauge and material.
- Energy Efficiency: Proper winding design minimizes losses, ensuring efficient power conversion.
- Heat Dissipation: Oil immersion helps regulate the temperature of the windings, preventing overheating and insulation degradation.
2. Types of Transformer Windings
Windings in oil-immersed transformers vary based on application, load requirements, and voltage levels. The table below outlines common winding types and their characteristics:
Winding Type | Structure | Advantages | Applications |
---|---|---|---|
Disc Winding | Conductors wound in disc-shaped coils | Even voltage distribution, low eddy current loss | High-voltage transformers |
Helical Winding | Helical turns around the core | High mechanical strength, good short-circuit withstand capability | Medium-voltage transformers |
Layer Winding | Conductors arranged in multiple layers | Compact design, effective cooling | Low-voltage applications |
Interleaved Winding | Alternating sections of primary and secondary windings | Reduced leakage reactance, improved efficiency | High-power applications |
- Disc windings are preferred for high-voltage applications due to their efficient voltage distribution.
- Helical windings provide excellent mechanical strength, making them suitable for high-current applications.
- Layer windings are commonly used in distribution transformers.
- Interleaved windings improve efficiency by reducing stray losses.
The choice of conductor material affects electrical conductivity, efficiency, and heat dissipation. The most commonly used materials are:
Material | Conductivity (S/m) | Thermal Conductivity (W/m·K) | Cost | Applications |
---|---|---|---|---|
Copper | 5.8 × 10⁷ | 401 | High | High-efficiency transformers |
Aluminum | 3.8 × 10⁷ | 237 | Lower | Cost-sensitive applications |
- Copper windings offer superior electrical and thermal conductivity, reducing resistive losses.
- Aluminum windings are lightweight and cost-effective but have higher resistance, leading to slightly increased losses.
Key Considerations for Material Selection:
- Efficiency requirements (copper is more efficient).
- Weight constraints (aluminum is lighter).
- Cost considerations (aluminum is cheaper but less conductive).
A. Insulation of Windings
Proper insulation prevents electrical breakdown and ensures longevity. Common insulation materials include:
Insulation Material | Dielectric Strength (kV/mm) | Thermal Stability | Application |
---|---|---|---|
Paper (Kraft) | 8–12 | Moderate | High-voltage transformers |
Nomex | 16 | High | High-temperature environments |
Epoxy Resin | 20 | Very High | Cast-resin transformers |
B. Cooling of Windings
Oil-immersed transformers rely on transformer oil for cooling. The oil circulates around the windings, absorbing and dissipating heat.
Cooling Methods:
- Natural Oil Circulation (ONAN) – Used in small to medium transformers.
- Forced Oil Circulation (OFAF) – Used in large transformers for enhanced cooling.
Proper insulation and cooling strategies prevent overheating, reduce dielectric stress, and extend transformer lifespan.
5. Losses Associated with Transformer Windings
Two major types of losses occur in windings:
A. Copper Loss (I²R Loss)
Copper loss results from resistance in the winding conductors and is calculated as:
[P = I^2 R]
Where:
- (P) = Power loss in watts
- (I) = Current in amperes
- (R) = Resistance in ohms
Reducing copper losses involves:
- Using low-resistance materials (copper).
- Increasing conductor cross-sectional area.
- Optimizing winding configuration.
B. Eddy Current Loss
Eddy currents are induced within conductors due to changing magnetic fields, causing localized heating. Laminated windings and specialized alloys help minimize these losses.
6. Winding Configurations and Their Impact on Performance
Transformer windings can be arranged in different configurations to optimize performance:
Winding Configuration | Features | Application |
---|---|---|
Delta (Δ) | High efficiency, balanced load distribution | Industrial and power grid applications |
Star (Y) | Neutral point availability, lower voltage per phase | Distribution networks |
Auto-Transformer | Single winding with variable tap points | Voltage regulation and motor start applications |
- Delta windings provide better fault tolerance.
- Star windings offer neutral grounding for safety.
- Auto-transformers allow variable voltage adjustment.
7. Common Winding Failures and Their Causes
Failure in transformer windings can lead to power outages and costly repairs. Common failure modes include:
Failure Type | Cause | Prevention |
---|---|---|
Short Circuits | Insulation breakdown | Use high-quality insulation materials |
Overheating | High current loads | Efficient cooling and oil maintenance |
Mechanical Deformation | Short-circuit forces | Reinforced winding structures |
Moisture Contamination | Oil degradation | Regular oil filtration and testing |
Why Is Insulating Oil Critical in Oil-Immersed Transformers?
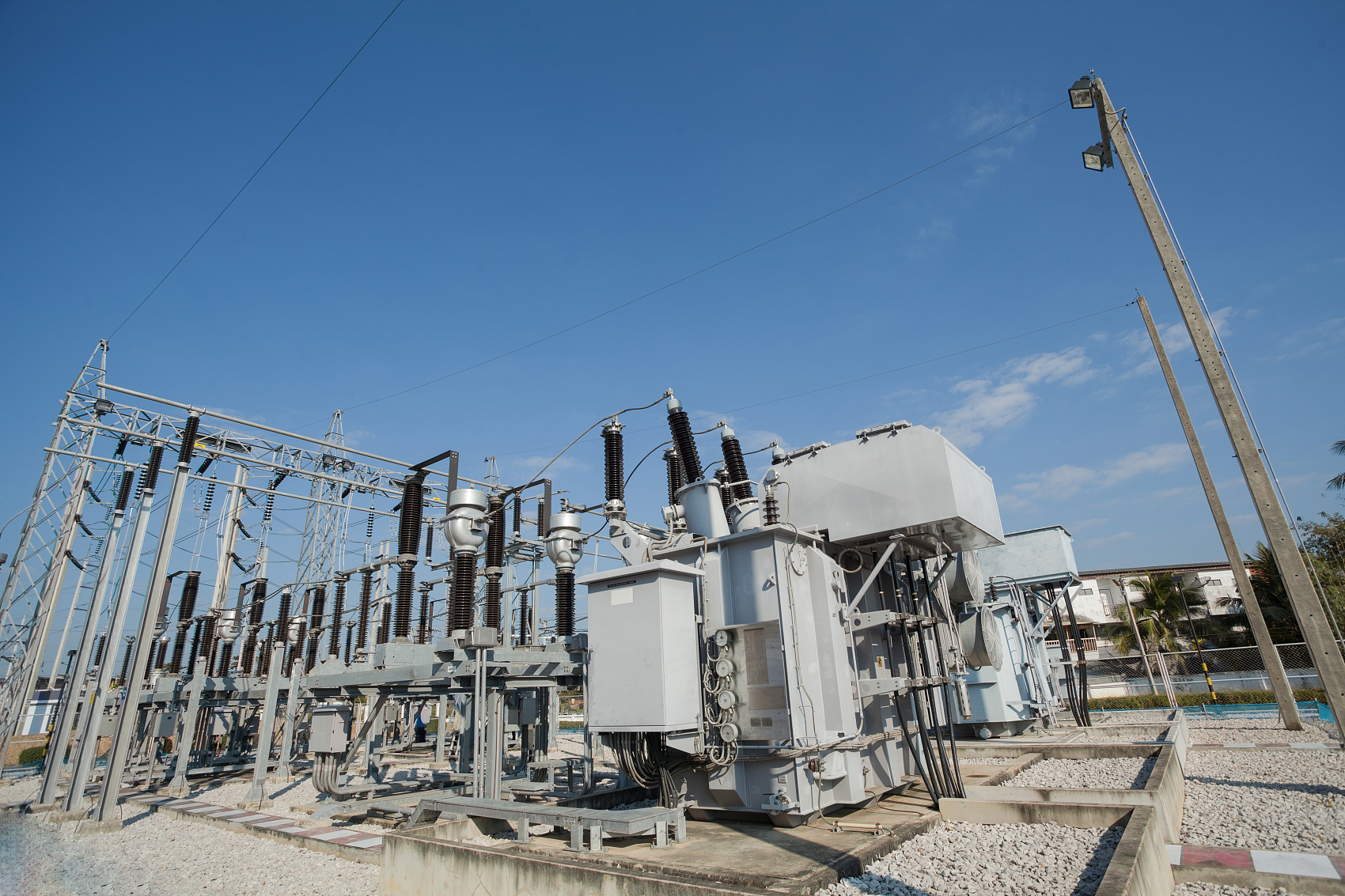
Oil-immersed transformers are widely used in power transmission and distribution due to their high efficiency and durability. However, without proper insulation and cooling, these transformers can overheat, short-circuit, or even fail catastrophically. Insulating oil is a vital component in ensuring the safe and efficient operation of these transformers. It prevents electrical breakdown, dissipates heat, and extends the transformer’s lifespan.
Insulating oil in an oil-immersed transformer serves as both a dielectric medium and a cooling agent. It prevents electrical discharge between high-voltage components, reduces overheating, and protects transformer windings from moisture and contamination. High-quality insulating oil enhances the transformer’s efficiency, reliability, and longevity.
Understanding the role of insulating oil is essential for transformer design, maintenance, and performance optimization. This article explores the critical functions, properties, and maintenance of insulating oil in oil-immersed transformers.
Insulating oil is only used for cooling in transformers.False
Insulating oil serves both as a dielectric medium and as a cooling agent, preventing electrical breakdown while dissipating heat.
1. Functions of Insulating Oil in Oil-Immersed Transformers
Insulating oil performs multiple crucial functions:
- Electrical Insulation: Prevents arcing and dielectric breakdown between windings.
- Cooling and Heat Dissipation: Absorbs and transfers heat away from the core and windings.
- Moisture Protection: Shields insulation materials from moisture, preventing degradation.
- Contaminant Removal: Suspends and removes particles that could cause electrical faults.
2. Properties of High-Quality Insulating Oil
For insulating oil to perform effectively, it must possess specific properties. The table below summarizes the essential characteristics of high-quality transformer oil:
Property | Importance | Typical Value for Mineral Oil |
---|---|---|
Dielectric Strength (kV) | Prevents electrical breakdown | >30 kV |
Viscosity (cSt) | Ensures efficient heat transfer | 8-15 cSt at 40°C |
Moisture Content (ppm) | Lower moisture ensures better insulation | <10 ppm |
Flash Point (°C) | Reduces fire risk | >140°C |
Pour Point (°C) | Ensures operation in cold environments | -40°C |
Acid Number (mg KOH/g) | Low acidity prevents corrosion | <0.05 |
- Dielectric strength determines the oil’s ability to withstand high voltages.
- Viscosity affects the oil’s ability to circulate and transfer heat.
- Moisture content must be minimal to maintain electrical insulation properties.
- Flash and pour points ensure safe operation in different temperatures.
3. Types of Insulating Oil
Insulating oils are classified based on their composition and application:
Type of Oil | Characteristics | Applications |
---|---|---|
Mineral Oil | Cost-effective, widely used | Power and distribution transformers |
Silicone Oil | High thermal stability, flame-resistant | Indoor and fire-prone environments |
Natural Ester (Vegetable Oil) | Biodegradable, moisture-resistant | Eco-friendly applications |
Synthetic Ester | High oxidation resistance, low flammability | Industrial and high-performance transformers |
- Mineral oils are commonly used due to their availability and cost-effectiveness.
- Silicone and ester oils are used in environmentally sensitive areas and high-temperature applications.
4. Cooling Mechanisms of Insulating Oil
Insulating oil removes heat through different cooling mechanisms:
Cooling Method | Description | Application |
---|---|---|
ONAN (Oil Natural Air Natural) | Oil circulates naturally; air-cooled externally | Small to medium transformers |
ONAF (Oil Natural Air Forced) | Natural oil circulation; external air fans enhance cooling | Medium to large transformers |
OFWF (Oil Forced Water Forced) | Oil is actively pumped; water-cooled system | Very high-power transformers |
Cooling efficiency directly affects transformer performance. The ONAF method is widely used for large transformers, where fans improve air circulation.
5. Degradation of Insulating Oil and Maintenance Practices
Over time, insulating oil degrades due to oxidation, moisture absorption, and contamination. Proper maintenance is essential to ensure long-term performance.
A. Causes of Oil Degradation
- Oxidation: Oxygen reacts with the oil, forming sludge and acids.
- Moisture Absorption: Water reduces dielectric strength, leading to electrical failure.
- Thermal Stress: High operating temperatures accelerate oil breakdown.
- Particle Contamination: Dust and metal particles lower insulation properties.
B. Monitoring and Testing Transformer Oil
Regular testing ensures the insulating oil maintains its properties. Below are essential tests:
Test Name | Purpose | Standard Limit |
---|---|---|
Dielectric Strength Test | Measures breakdown voltage | >30 kV |
Moisture Content Test | Detects water contamination | <10 ppm |
Acid Number Test | Assesses oil acidity | <0.05 mg KOH/g |
Interfacial Tension Test | Indicates oil degradation | >25 mN/m |
Routine oil sampling and analysis help detect contamination and degradation early.
C. Oil Filtration and Regeneration
To restore oil quality, transformers undergo:
- Filtration – Removes solid contaminants and water.
- Degassing – Eliminates dissolved gases that lower insulation strength.
- Reconditioning – Neutralizes acids and restores oil properties.
Oil regeneration extends transformer life by restoring insulation oil to near-original quality.
6. Fire Safety and Environmental Considerations
Transformer oil must meet fire safety and environmental standards. Below are key considerations:
Risk Factor | Solution |
---|---|
Fire Hazard | Use high-flash-point or flame-retardant oils |
Oil Leaks | Ensure proper tank sealing and monitoring |
Environmental Impact | Use biodegradable natural ester oils |
Proper containment and spill management prevent environmental contamination.
7. Common Failures Due to Poor Insulating Oil Management
Failure to maintain insulating oil can lead to transformer malfunctions. Below are some common failures:
Failure Type | Cause | Consequence |
---|---|---|
Electrical Breakdown | Low dielectric strength | Transformer failure |
Overheating | Poor heat dissipation | Insulation damage |
Corrosion | Acidic oil | Core and winding degradation |
Fire Hazard | Low flash point | Risk of explosion |
Preventive maintenance ensures transformers operate safely and efficiently.
How Do the Core, Windings, and Oil Interact for Optimal Transformer Performance?
Transformers are the backbone of electrical power distribution, converting voltage levels efficiently to ensure stable power transmission. Within an oil-immersed transformer, three key components—the core, windings, and insulating oil—work together in a delicate balance to ensure optimal efficiency, cooling, and insulation. If one of these components fails or operates inefficiently, the entire transformer system is compromised, leading to power losses, overheating, and potential failures.
The core, windings, and insulating oil interact synergistically in an oil-immersed transformer to enable efficient electromagnetic energy conversion, minimize losses, and regulate temperature. The core channels magnetic flux, the windings conduct electrical current, and the oil provides cooling and electrical insulation. Their combined operation ensures reliable transformer performance and longevity.
To fully understand how these components interact, we need to examine their individual roles, the physics governing their function, and how their interactions optimize performance.
The core, windings, and oil function independently in an oil-immersed transformer.False
These three components work together, with the core facilitating magnetic flux, windings conducting current, and oil providing insulation and cooling.
1. The Core’s Role in Transformer Operation
The core is the magnetic circuit that enables efficient electromagnetic induction between the primary and secondary windings. Its key functions include:
- Guiding Magnetic Flux: The core provides a low-reluctance path for the magnetic field generated by the primary winding, ensuring efficient energy transfer to the secondary winding.
- Minimizing Core Losses: Using laminated silicon steel or amorphous metal reduces eddy current and hysteresis losses, improving efficiency.
- Providing Structural Integrity: The core supports the winding arrangement while maintaining electrical isolation.
Core Materials and Their Impact on Efficiency
The choice of core material affects transformer efficiency. Below is a comparison of common core materials:
Core Material | Magnetic Permeability | Eddy Current Loss | Hysteresis Loss | Common Use |
---|---|---|---|---|
Silicon Steel | High | Low | Moderate | Power Distribution |
Amorphous Metal | Very High | Very Low | Low | Energy-Efficient Transformers |
Ferrite | Moderate | Negligible | Low | High-Frequency Transformers |
A high-quality core ensures better electromagnetic performance, reducing power losses and enhancing transformer lifespan.
2. Windings: The Conduits of Electrical Energy
Transformer windings are responsible for voltage transformation through electromagnetic induction. Their main roles include:
- Conducting Electrical Current: The primary winding receives alternating current (AC) and generates a magnetic field, which induces a voltage in the secondary winding.
- Regulating Voltage and Current: The ratio of primary to secondary turns determines whether the transformer steps up or steps down voltage.
- Minimizing Resistive Losses: Using high-conductivity materials like copper reduces I²R (copper) losses.
Types of Winding Configurations
The way windings are arranged impacts efficiency and performance. Below are common winding types:
Winding Type | Structure | Advantages | Application |
---|---|---|---|
Disc Winding | Conductors wound in disc-shaped coils | Even voltage distribution, low eddy current loss | High-voltage transformers |
Helical Winding | Helical turns around the core | High mechanical strength | Medium-voltage transformers |
Layer Winding | Conductors in multiple layers | Compact design, effective cooling | Low-voltage applications |
Using copper instead of aluminum in windings improves electrical conductivity, reducing resistance and energy losses.
3. The Role of Insulating Oil in Transformer Performance
Insulating oil is critical for maintaining electrical insulation and thermal regulation in the transformer. Its functions include:
- Dielectric Insulation: Prevents short circuits by insulating high-voltage windings from the core and transformer tank.
- Cooling Mechanism: Absorbs and dissipates heat generated by the core and windings.
- Moisture and Contaminant Protection: Prevents insulation degradation due to moisture absorption.
Comparison of Insulating Oils
Different types of insulating oils offer unique advantages based on their properties:
Type of Oil | Dielectric Strength (kV) | Thermal Stability | Fire Resistance | Application |
---|---|---|---|---|
Mineral Oil | >30 | Moderate | Low | Standard power transformers |
Silicone Oil | >50 | High | High | Fire-sensitive environments |
Natural Ester Oil | >35 | High | Medium | Eco-friendly applications |
Using high-quality, low-moisture insulating oil prevents electrical breakdown and improves transformer longevity.
4. Interactions Between Core, Windings, and Oil
For optimal transformer performance, these three components must work in harmony. The following interactions are crucial:
A. Magnetic Flux Generation and Conduction
- The primary winding generates a magnetic field that the core channels efficiently to the secondary winding.
- Low-reluctance materials in the core ensure minimal magnetic losses.
- Excessive core saturation can lead to overheating and inefficiencies, requiring better core material selection.
B. Heat Generation and Cooling Management
- Windings and the core generate heat due to copper losses (I²R) and core losses (hysteresis and eddy currents).
- Insulating oil absorbs and dissipates heat, preventing overheating.
- Oil cooling methods such as ONAN (natural cooling) or ONAF (forced cooling with fans) enhance performance.
C. Electrical Insulation and Dielectric Stability
- The insulating oil prevents short circuits by maintaining electrical separation between windings and the core.
- Deteriorated oil with high moisture content can cause dielectric failure.
- Regular oil testing ensures high dielectric strength, reducing electrical breakdown risks.
5. Common Transformer Failures Due to Poor Component Interaction
If the core, windings, or oil do not function optimally together, transformer efficiency drops, leading to failures:
Failure Type | Cause | Prevention |
---|---|---|
Overheating | Poor oil circulation, excessive core losses | Use high-efficiency core materials and maintain oil cooling |
Electrical Breakdown | Degraded oil insulation, moisture ingress | Regular oil filtration and dielectric testing |
Winding Degradation | Overloading, excessive temperature rise | Proper load management and cooling system maintenance |
Core Saturation | Improper core material selection | Optimize core design for flux distribution |
Routine monitoring, oil testing, and preventive maintenance are crucial in avoiding transformer failures.
What Are the Key Maintenance Practices for Oil-Immersed Transformers?
Oil-immersed transformers are critical in power transmission and distribution systems, ensuring reliable voltage conversion. However, without proper maintenance, these transformers can suffer from oil degradation, overheating, insulation failure, and electrical breakdowns, leading to costly repairs or catastrophic failures. Implementing a proactive maintenance strategy is essential to enhance efficiency, extend lifespan, and prevent unplanned downtime.
Key maintenance practices for oil-immersed transformers include regular oil testing, thermal management, insulation inspections, load monitoring, and preventive maintenance schedules. These ensure dielectric strength, cooling efficiency, and overall transformer reliability. Regular diagnostics help detect issues early, preventing costly failures and downtime.
Understanding these maintenance practices is crucial for power engineers, facility managers, and maintenance teams to ensure transformer longevity and performance.
Oil-immersed transformers require no maintenance if oil levels are stable.False
Regular maintenance is necessary, including oil quality checks, temperature monitoring, and insulation inspections, to prevent failures.
1. Routine Inspections and Visual Checks
Regular inspections help detect leaks, corrosion, insulation wear, and overheating before they lead to major failures. Key checks include:
- Oil Level Inspection: Ensure proper oil levels in the conservator tank to maintain cooling and insulation.
- Leak Detection: Inspect gaskets, seals, and bushings for signs of oil leaks, which can reduce insulation effectiveness.
- Temperature Monitoring: Measure winding and oil temperatures to prevent thermal stress and overheating.
- Bushing and Insulator Condition: Look for cracks, dirt accumulation, or tracking marks, which can lead to electrical faults.
Inspection Frequency:
Transformer Type | Inspection Frequency |
---|---|
Distribution Transformers | Monthly |
Power Transformers | Weekly |
High-Voltage Transformers | Daily |
Routine inspections reduce the risk of unplanned outages by identifying minor issues before they escalate.
2. Transformer Oil Testing and Maintenance
Transformer oil serves as both an insulator and a coolant, and its properties degrade over time. Regular oil testing ensures dielectric strength, thermal stability, and moisture resistance.
A. Key Oil Tests and Their Importance
Test Name | Purpose | Acceptable Limit |
---|---|---|
Dielectric Strength Test | Measures oil’s ability to prevent arcing | >30 kV |
Moisture Content Test | Identifies water contamination | <10 ppm |
Acid Number Test | Determines oil acidity (higher acidity leads to insulation degradation) | <0.05 mg KOH/g |
Dissolved Gas Analysis (DGA) | Detects gases from electrical arcing and overheating | Varies based on gas type |
Regular oil sampling and testing prevent electrical insulation breakdown and cooling inefficiency.
B. Oil Filtration and Purification
Degraded oil must be filtered and regenerated to remove contaminants. The following steps restore oil quality:
- Filtration: Removes particulate matter and sludge.
- Degassing: Eliminates dissolved gases that could cause arcing.
- Dehydration: Extracts moisture to maintain dielectric strength.
Replacing or reconditioning oil every 5 to 7 years enhances transformer efficiency.
3. Cooling System Maintenance
Efficient heat dissipation prevents overheating and thermal stress on transformer components. Key cooling maintenance tasks include:
- Checking Radiators and Fans: Ensure proper airflow in forced-air cooling systems.
- Cleaning Cooling Tubes: Remove dust and sludge to maintain oil circulation.
- Verifying Thermostats and Cooling Controls: Ensure automatic cooling mechanisms function correctly.
Cooling System Types and Maintenance Needs
Cooling Method | Common Issues | Maintenance Action |
---|---|---|
ONAN (Oil Natural Air Natural) | Clogged radiators | Clean and inspect annually |
ONAF (Oil Natural Air Forced) | Fan motor failure | Test fans monthly |
OFWF (Oil Forced Water Forced) | Water leakage, pump failure | Inspect pumps and heat exchangers quarterly |
Effective cooling maintenance prevents insulation damage and extends transformer life.
4. Electrical and Insulation Testing
The insulation system (windings, bushings, and oil) must maintain its integrity to prevent short circuits and power failures.
A. Key Electrical Tests
Test Name | Purpose | Recommended Interval |
---|---|---|
Insulation Resistance Test (Megger Test) | Checks winding-to-ground insulation | Yearly |
Polarization Index (PI) Test | Measures insulation aging | Every 3 years |
Power Factor Test | Evaluates insulation losses | Every 3 years |
Poor insulation resistance indicates moisture ingress or deterioration of dielectric materials.
B. Bushing and Winding Maintenance
- Clean Bushings: Prevent contamination and tracking.
- Check Tap Changer Contacts: Ensure voltage regulation operates efficiently.
- Tighten Electrical Connections: Loose connections cause overheating and arcing.
5. Load and Overload Management
Operating transformers beyond their rated load capacity causes thermal degradation and shortens their lifespan. Effective load management includes:
- Monitoring Load Currents: Ensure loads remain within safe limits.
- Balancing Phases: Unequal loads cause voltage fluctuations and overheating.
- Recording Load Trends: Detect potential overloading issues early.
Transformer Load Capacity Limits
Transformer Rating | Safe Load Range (Max) |
---|---|
100 kVA | 90-100% |
500 kVA | 85-95% |
1000 kVA | 80-90% |
Avoiding overloads reduces winding stress and prevents insulation breakdown.
6. Preventive Maintenance Scheduling
A structured maintenance schedule ensures continuous transformer reliability. Below is a sample preventive maintenance plan:
Maintenance Task | Frequency |
---|---|
Visual Inspection | Monthly |
Oil Sampling & Testing | Every 6 months |
Cooling System Check | Quarterly |
Insulation Resistance Test | Annually |
Load Analysis | Continuous Monitoring |
Following a planned maintenance schedule improves efficiency and reduces the risk of sudden failures.
7. Addressing Common Transformer Failures
If not properly maintained, transformers can experience severe failures. Below are common issues and their solutions:
Failure Type | Cause | Solution |
---|---|---|
Oil Degradation | Oxidation, moisture contamination | Perform oil filtration and replacement |
Overheating | Poor cooling efficiency | Clean radiators, inspect fans, and maintain oil levels |
Short Circuits | Insulation failure | Regular insulation testing and bushing inspections |
Load Imbalance | Unequal phase loading | Balance loads and monitor current distribution |
Proactive maintenance prevents failures and extends transformer lifespan.
Conclusion
The seamless interaction between the core, windings, and oil is what makes oil-immersed transformers both efficient and reliable. By understanding the functions of each component and implementing proper maintenance, operators can ensure longevity and optimal performance.