Transformer oil plays a crucial role in insulating and cooling oil-immersed transformers, ensuring their efficiency and longevity. However, improper oil selection, contamination, or lack of maintenance can lead to insulation failure, overheating, and transformer breakdowns. Many operators overlook the importance of regular oil testing and maintenance, which can result in costly repairs and unexpected downtime.
This article explores the different types of transformer oil, the key testing methods used to assess its condition, and best practices for maintaining oil quality to ensure transformer reliability and performance.
What Are the Different Types of Transformer Oil and How Do They Compare?
Transformer oil is a critical insulating and cooling medium in oil-immersed transformers. The type of oil used significantly affects dielectric strength, thermal stability, oxidation resistance, and environmental impact. Choosing the right transformer oil enhances efficiency, reliability, and lifespan, while improper selection can lead to insulation breakdown, overheating, and transformer failure.
The main types of transformer oil include mineral oil (naphthenic and paraffinic), silicone oil, and natural ester oil. These oils differ in terms of dielectric strength, oxidation resistance, fire safety, and environmental sustainability. Mineral oils are cost-effective but have lower fire resistance, while synthetic and ester-based oils offer better fire safety and biodegradability.
This guide explores different transformer oil types, their properties, and comparative advantages for various applications.
All transformer oils have similar properties and performance.False
Different transformer oils have distinct characteristics affecting insulation performance, thermal stability, oxidation resistance, fire safety, and environmental impact.
1. Types of Transformer Oil
A. Mineral Oil (Petroleum-Based)
Mineral oil is the most widely used transformer oil, derived from crude oil. It is classified into two types based on its molecular structure:
Type | Composition | Characteristics | Common Use |
---|---|---|---|
Naphthenic Oil | High in naphthenes (cycloparaffins) | Excellent low-temperature performance, good oxidation stability | High-voltage transformers, colder climates |
Paraffinic Oil | High in paraffins (straight-chain hydrocarbons) | High oxidation stability but forms sludge over time | Medium-voltage transformers, warmer climates |
Advantages of Mineral Oil:
✅ High dielectric strength (30-50 kV) for effective insulation.
✅ Good heat dissipation for cooling transformer windings.
✅ Proven and widely available with low cost.
Disadvantages of Mineral Oil:
❌ Flammable, increasing fire risk.
❌ Environmental concerns, as it is non-biodegradable.
❌ Forms sludge over time, reducing efficiency.
B. Silicone Oil (Synthetic-Based)
Silicone oil is a synthetic insulating fluid with high fire resistance and thermal stability.
Key Properties:
- Self-extinguishing with a high fire point (~450°C).
- Resistant to oxidation with long service life (~30 years).
- Low environmental toxicity and good biodegradability.
Applications:
✔ Fire-prone areas (e.g., urban substations, industrial plants).
✔ Transformers inside buildings where fire safety is a concern.
Comparison to Mineral Oil:
Property | Silicone Oil | Mineral Oil |
---|---|---|
Fire Safety | ✅ High (Self-extinguishing) | ❌ Low (Flammable) |
Oxidation Stability | ✅ Excellent | ❌ Moderate (sludge formation) |
Dielectric Strength | ✅ ~50 kV | ✅ 30-50 kV |
Environmental Impact | ✅ Biodegradable | ❌ Non-biodegradable |
❌ Silicone oil is more expensive and may not be suitable for cost-sensitive applications.
C. Natural Ester Oil (Vegetable-Based)
Natural ester oils, derived from vegetable sources, are biodegradable, non-toxic, and fire-resistant.
Key Properties:
- High moisture tolerance, reducing insulation degradation.
- Non-toxic and environmentally friendly.
- Slower oxidation rate, extending oil service life.
Applications:
✔ Eco-sensitive areas (renewable energy projects, rural grids).
✔ Indoor transformers requiring fire-resistant oils.
✔ High-humidity environments due to moisture absorption capability.
Comparison to Mineral Oil:
Property | Natural Ester Oil | Mineral Oil |
---|---|---|
Fire Safety | ✅ High (High flash point) | ❌ Low |
Biodegradability | ✅ Yes (Non-toxic) | ❌ No (Petroleum-based) |
Moisture Handling | ✅ Absorbs moisture | ❌ Poor moisture tolerance |
Oxidation Stability | ✅ High | ❌ Moderate |
❌ Higher cost and potential viscosity issues at low temperatures.
D. Synthetic Ester Oil
Synthetic esters are engineered fluids that offer higher thermal and oxidation stability than natural esters.
Key Properties:
- Excellent fire safety and biodegradability.
- Longer service life compared to mineral oil.
- Higher cost than natural esters.
Applications:
✔ High-performance transformers in industrial and renewable energy sectors.
✔ Long-life transformers where reduced maintenance is required.
Comparison to Natural Ester:
Property | Synthetic Ester | Natural Ester |
---|---|---|
Oxidation Stability | ✅ Higher | ❌ Lower |
Moisture Absorption | ✅ Moderate | ✅ High |
Environmental Impact | ✅ Biodegradable | ✅ Biodegradable |
Cost | ❌ Higher | ✅ Lower |
✅ Best option for environmentally sustainable and high-performance transformers.
2. Comparative Analysis of Transformer Oils
A. Key Performance Comparison
Property | Mineral Oil | Silicone Oil | Natural Ester Oil | Synthetic Ester Oil |
---|---|---|---|---|
Dielectric Strength | 30-50 kV | 50 kV | 40-50 kV | 50-55 kV |
Fire Point | ~170°C | ~450°C | ~300°C | ~320°C |
Oxidation Stability | Moderate | Excellent | Good | Excellent |
Moisture Handling | Poor | Moderate | High | Moderate |
Environmental Impact | Non-biodegradable | Biodegradable | Biodegradable | Biodegradable |
Cost | Low | High | Moderate | High |
B. Choosing the Right Transformer Oil
Application | Recommended Oil Type | Reason |
---|---|---|
General Power Grids | Naphthenic Mineral Oil | Cost-effective, widely available |
Indoor Transformers | Silicone Oil / Natural Ester | High fire safety, low toxicity |
Renewable Energy Projects | Natural Ester / Synthetic Ester | Eco-friendly, high moisture tolerance |
Industrial High-Load Transformers | Synthetic Ester / Silicone Oil | High thermal stability, long lifespan |
Cold Climate Transformers | Naphthenic Mineral Oil | Good low-temperature performance |
✅ Selecting the right oil enhances transformer safety, efficiency, and durability.
3. Key Maintenance Considerations for Transformer Oil
Regardless of oil type, regular maintenance is essential to ensure insulation performance and prevent failures.
A. Oil Testing Schedule
Test | Frequency | Purpose |
---|---|---|
Dielectric Strength Test | Every 6-12 months | Ensures insulation capability |
Dissolved Gas Analysis (DGA) | Yearly | Detects internal faults |
Moisture Content Test | Yearly | Prevents insulation degradation |
Acid Number (TAN) Test | Yearly | Monitors oil aging |
B. Common Transformer Oil Issues and Solutions
Issue | Cause | Solution |
---|---|---|
Low Dielectric Strength | Moisture contamination | Perform oil filtration |
High Acidity | Oxidation and sludge formation | Replace oil |
Overheating | Poor cooling system performance | Clean radiators, check airflow |
Gas Formation | Internal arcing or thermal stress | Conduct DGA and investigate faults |
✅ Regular monitoring prevents transformer failures and extends oil service life.
Why Is Transformer Oil Essential for Insulation and Cooling?
Oil-immersed transformers play a critical role in power transmission and distribution networks, ensuring efficient voltage conversion. One of the most vital components of these transformers is transformer oil, which acts as both an insulator and a cooling medium. Without transformer oil, electrical insulation would degrade, overheating would increase, and transformer lifespan would be significantly reduced.
Transformer oil is essential for insulation and cooling because it prevents electrical breakdown, dissipates heat, absorbs moisture, and enhances transformer longevity. Its high dielectric strength ensures proper insulation, while its thermal conductivity efficiently transfers heat away from windings and the core. Proper oil maintenance prevents failures and extends transformer life.
This guide explores the functions, properties, and importance of transformer oil in maintaining efficient and reliable transformer operation.
Transformer oil only serves as a cooling medium and has no impact on insulation.False
Transformer oil provides both insulation and cooling, preventing electrical breakdown and maintaining safe operating temperatures.
1. The Dual Role of Transformer Oil: Insulation and Cooling
A. Electrical Insulation Properties
Why it matters: Transformers operate at high voltages, and insulation failure can lead to short circuits, electrical arcs, and transformer damage.
✅ Transformer oil prevents direct contact between electrical components, ensuring safe operation.
✅ Its high dielectric strength (30-50 kV) helps resist electrical breakdown.
✅ Absorbs moisture, which would otherwise weaken insulation strength.
Property | Role in Insulation |
---|---|
Dielectric Strength | Prevents arcing between transformer windings |
Moisture Absorption | Protects solid insulation from degradation |
Chemical Stability | Prevents formation of conductive contaminants |
B. Thermal Management and Cooling Function
Why it matters: Transformer windings and core generate heat during operation, and excess heat reduces efficiency and damages insulation.
✅ Transformer oil absorbs and transfers heat away from windings and core.
✅ Prevents overheating and thermal stress on insulation materials.
✅ Ensures even temperature distribution across the transformer.
Cooling Function | Effect |
---|---|
Heat Absorption | Prevents windings from overheating |
Circulation Through Radiators | Maintains stable operating temperature |
Supports Forced Cooling Systems | Works with cooling fans or pumps in large transformers |
💡 Without proper cooling, transformer lifespan decreases due to insulation deterioration.
2. Key Properties That Make Transformer Oil Effective
Transformer oil must possess specific properties to function effectively as both an insulator and coolant.
Property | Purpose | Ideal Value |
---|---|---|
Dielectric Strength | Prevents electrical breakdown | >30 kV |
Thermal Conductivity | Transfers heat efficiently | High |
Moisture Content | Keeps insulation dry | <10 ppm |
Oxidation Stability | Prevents sludge formation | High |
💡 Maintaining these properties through regular oil testing is essential for transformer performance.
3. Types of Transformer Oil and Their Insulation & Cooling Performance
Different types of transformer oils provide varying levels of insulation and cooling efficiency.
Oil Type | Insulation Strength | Cooling Efficiency | Fire Safety | Environmental Impact |
---|---|---|---|---|
Naphthenic Mineral Oil | High | Good | Moderate | Non-biodegradable |
Paraffinic Mineral Oil | Moderate | High | Moderate | Non-biodegradable |
Silicone Oil | Excellent | Moderate | High (Self-extinguishing) | Biodegradable |
Natural Ester Oil | High | Moderate | High | Fully biodegradable |
✅ Mineral oils are widely used due to cost-effectiveness.
✅ Silicone oils are preferred for fire-prone areas.
✅ Natural esters provide an eco-friendly alternative with good insulation.
4. How Transformer Oil Prevents Failures and Ensures Longevity
Transformer oil degradation leads to increased risk of failure. Proper oil maintenance is key to long-term reliability.
A. Common Transformer Oil Issues
Issue | Cause | Consequence |
---|---|---|
Low Dielectric Strength | Moisture contamination | Insulation breakdown |
Oil Sludge Formation | Oxidation over time | Blocks cooling pathways |
High Acidity | Chemical aging | Corrodes internal components |
Dissolved Gas Accumulation | Arcing, overheating | Internal faults and failure |
B. Preventive Measures
✅ Regular oil testing (dielectric strength, DGA, moisture content).
✅ Filtration and purification to remove sludge and moisture.
✅ Replacing degraded oil before insulation breakdown occurs.
💡 Well-maintained transformer oil can extend transformer life by 20-30 years.
5. Transformer Oil Testing and Maintenance Best Practices
A. Key Transformer Oil Tests
Test | Purpose | Frequency | Acceptable Limit |
---|---|---|---|
Dielectric Strength Test | Ensures insulation capability | Every 6-12 months | >30 kV |
Dissolved Gas Analysis (DGA) | Detects arcing, overheating | Yearly | Gas-specific limits |
Moisture Content Test | Prevents insulation degradation | Yearly | <10 ppm |
Acidity (TAN Test) | Monitors oil aging | Yearly | <0.05 mg KOH/g |
✅ Regular testing identifies faults before they lead to transformer failure.
B. Oil Filtration and Regeneration
Even high-quality transformer oil degrades over time. Proper filtration removes moisture, gases, and solid contaminants to restore performance.
Maintenance Action | Purpose | Frequency |
---|---|---|
Vacuum Filtration | Removes moisture and dissolved gases | Every 3-5 years |
Centrifugal Separation | Eliminates solid contaminants | As needed |
Oil Regeneration | Restores chemical properties | Every 5-7 years |
Complete Oil Replacement | Replaces degraded oil | Every 10-15 years |
✅ Maintaining clean oil ensures long-term insulation reliability.
What Are the Key Tests Used to Assess Transformer Oil Quality?
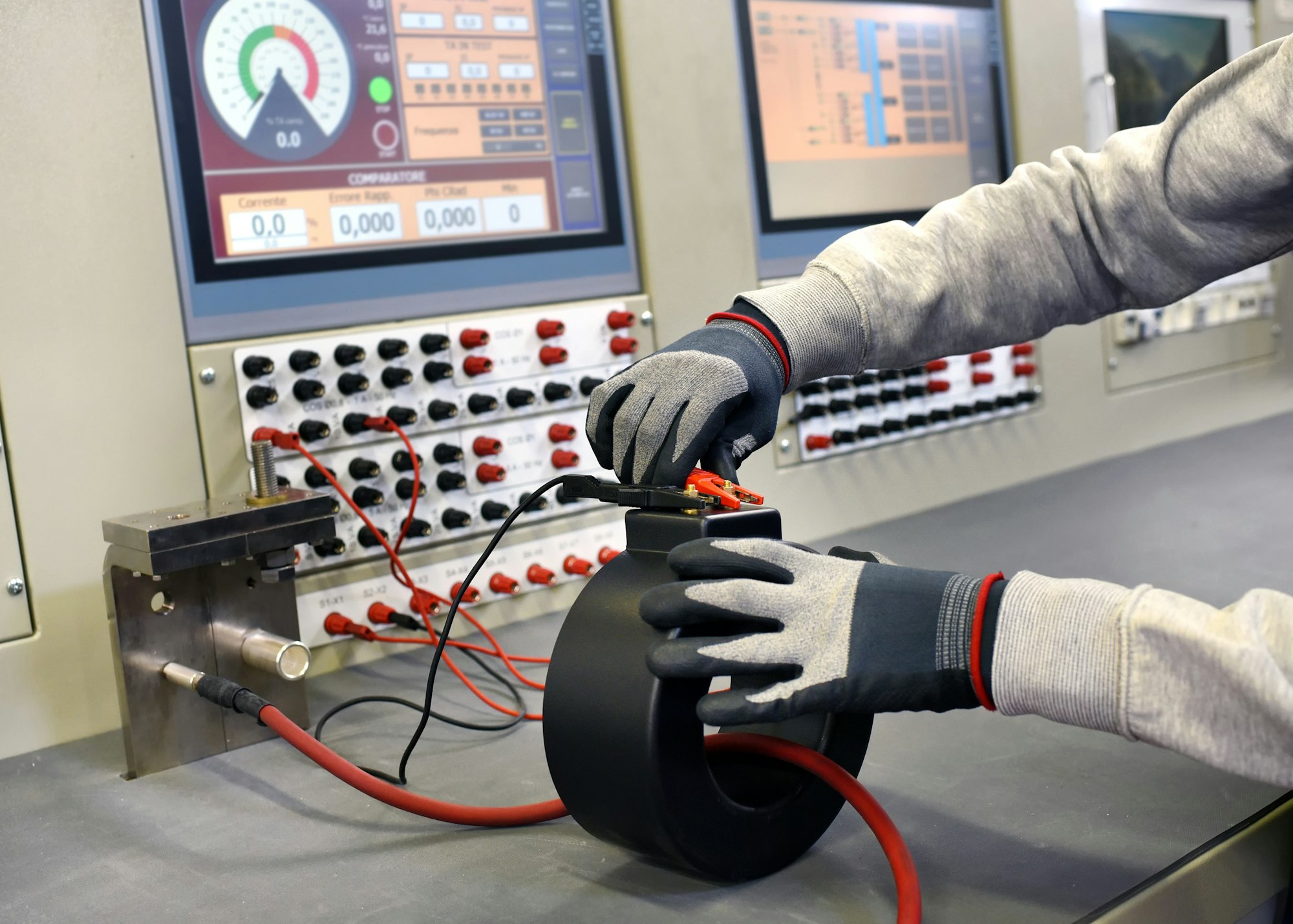
Transformer oil is essential for insulation, cooling, and fault protection in oil-immersed transformers. However, contaminants such as moisture, oxidation byproducts, and dissolved gases can degrade its performance over time. Regular oil testing is critical to detect early signs of oil degradation, ensuring transformer efficiency, longevity, and reliability.
Key tests used to assess transformer oil quality include dielectric strength testing, micro water content measurement, oil medium loss analysis, and chromatographic analysis. These tests help identify insulation breakdown risks, moisture contamination, aging effects, and dissolved gas levels, preventing transformer failures and extending operational life.
This guide explores essential transformer oil tests, their purpose, procedures, and importance in maintaining high-performance insulation and cooling.
Transformer oil testing is unnecessary as long as the transformer is operational.False
Regular transformer oil testing is crucial to detect early signs of degradation, preventing failures and extending transformer lifespan.
1. Why Is Transformer Oil Testing Important?
Transformer oil testing helps:
✅ Ensure strong insulation performance by maintaining high dielectric strength.
✅ Prevent moisture-induced failures by detecting micro water content.
✅ Identify oil degradation through medium loss analysis.
✅ Detect early faults using chromatographic analysis of dissolved gases.
💡 Regular oil testing can extend transformer life by 30-50% and prevent costly failures.
2. Key Transformer Oil Tests for Quality Assessment
A. Dielectric Strength Test (Breakdown Voltage Test)
Purpose: Measures the ability of transformer oil to withstand high voltage without electrical breakdown.
Test Parameter | Acceptable Limit |
---|---|
Breakdown Voltage (BDV) | >30 kV (New Oil), >25 kV (Used Oil) |
Procedure:
- Place the transformer oil sample between two electrodes.
- Gradually increase voltage until an electrical breakdown occurs.
- Record the voltage at which breakdown happens.
✅ Pass if BDV is above 30 kV, ensuring strong insulation properties.
❌ Fail if BDV is low, indicating moisture or particle contamination.
B. Micro Water Content Test
Purpose: Detects water contamination in transformer oil, which reduces insulation effectiveness.
Test Parameter | Acceptable Limit |
---|---|
Water Content | <10 ppm |
Procedure:
- Use Karl Fischer titration or moisture sensors to measure water content.
- Compare results with the acceptable moisture limit.
✅ Pass if water content is below 10 ppm.
❌ Fail if moisture levels are high, requiring oil filtration or drying.
💡 Water contamination is a major cause of insulation failure in transformers.
C. Oil Medium Loss Test (Dielectric Dissipation Factor Test - Tan Delta Test)
Purpose: Evaluates the dielectric loss and aging condition of transformer oil.
Test Parameter | Acceptable Limit |
---|---|
Dissipation Factor (Tan δ at 90°C) | <0.005 |
Procedure:
- Apply an AC voltage to the oil sample.
- Measure the phase angle shift and energy loss in the oil.
- Calculate the dissipation factor (Tan δ).
✅ Pass if Tan δ is within limits, indicating minimal energy loss.
❌ Fail if Tan δ is high, suggesting oil oxidation and insulation degradation.
💡 A rising dissipation factor signals oil aging, requiring purification or replacement.
D. Oil Chromatographic Analysis (Dissolved Gas Analysis - DGA)
Purpose: Detects early faults by analyzing dissolved gases in transformer oil.
Gas Detected | Cause of Transformer Issue | Warning Level (ppm) |
---|---|---|
Hydrogen (H₂) | Partial discharge inside transformer | >100 ppm |
Methane (CH₄) | Minor overheating of oil | >120 ppm |
Ethylene (C₂H₄) | Severe overheating | >150 ppm |
Acetylene (C₂H₂) | Arcing and insulation failure | Any presence is critical |
Procedure:
- Extract transformer oil sample.
- Analyze dissolved gases using gas chromatography.
- Compare results with normal operating values.
✅ Pass if gas levels are within normal limits.
❌ Fail if acetylene is detected, indicating serious arcing or overheating.
💡 DGA is the most effective method for early fault detection in transformers.
3. Recommended Transformer Oil Testing Frequency
Test | Frequency | Purpose |
---|---|---|
Dielectric Strength Test (BDV) | Every 6-12 months | Ensures insulation capability |
Micro Water Content Test | Yearly | Detects moisture contamination |
Oil Medium Loss (Tan δ Test) | Yearly | Identifies oil degradation |
Oil Chromatographic Analysis (DGA) | Yearly | Detects internal faults |
✅ Regular oil testing helps prevent transformer failures and costly repairs.
4. Best Practices for Transformer Oil Maintenance
A. Oil Filtration and Purification
Purpose: Removes moisture, gases, and solid contaminants to restore oil quality.
Filtration Method | Purpose | Frequency |
---|---|---|
Vacuum Filtration | Removes moisture and dissolved gases | Every 3-5 years |
Centrifugal Separation | Eliminates solid contaminants | As needed |
✅ Filtration restores oil quality without requiring full replacement.
B. Moisture Prevention Measures
- Replace silica gel breathers when color changes from blue to pink.
- Inspect transformer seals and gaskets regularly.
- Store transformer oil in clean, dry containers.
✅ Preventing moisture contamination extends oil and transformer lifespan.
C. Cooling System Optimization
- Clean radiators and cooling fans to maintain heat dissipation.
- Ensure proper oil circulation and check for blockages.
- Monitor oil temperature and cooling system performance.
✅ Proper cooling prevents overheating and oil degradation.
5. Common Transformer Oil Issues and Solutions
Issue | Cause | Solution |
---|---|---|
Low Dielectric Strength | Moisture contamination | Perform oil filtration |
High Acidity (TAN Test Fail) | Oxidation and sludge formation | Replace oil |
Overheating | Poor cooling system performance | Clean radiators and fans |
Dissolved Gases Detected | Arcing, overheating, or internal faults | Perform DGA and investigate faults |
✅ Addressing oil issues early prevents transformer failures and repair costs.
How Does Oil Contamination Affect Transformer Performance?
Transformer oil is essential for insulation, cooling, and fault detection in oil-immersed transformers. However, over time, contamination from moisture, sludge, acids, and dissolved gases reduces its effectiveness. Contaminated oil leads to insulation breakdown, overheating, and increased failure risks, severely impacting transformer performance.
Oil contamination in transformers degrades insulation strength, increases thermal stress, accelerates component aging, and promotes internal faults. Key contaminants such as moisture, sludge, acids, and gases reduce dielectric strength, cause overheating, and increase maintenance costs. Regular oil testing and filtration prevent performance degradation and extend transformer lifespan.
This guide explains how different contaminants affect transformer oil and performance, their consequences, and preventive maintenance strategies.
Transformer oil contamination has little impact on transformer performance.False
Oil contamination significantly reduces insulation strength, causes overheating, and accelerates transformer aging, leading to increased failure risks.
1. Types of Transformer Oil Contamination and Their Effects
A. Moisture Contamination
How it occurs:
- Absorption from air (especially in humid environments).
- Leaks in oil tanks or deteriorated gaskets.
- Aging solid insulation releasing moisture.
Effect | Consequence |
---|---|
Reduces dielectric strength | Increased risk of insulation breakdown. |
Promotes oxidation | Leads to acidic oil and sludge formation. |
Forms conductive paths | Increases chances of short circuits. |
✅ Moisture contamination is the leading cause of insulation failure.
B. Sludge and Sediment Formation
How it occurs:
- Oxidation of oil over time.
- Chemical reactions with metal components.
- Breakdown of cellulose insulation.
Effect | Consequence |
---|---|
Clogs cooling ducts and radiators | Leads to overheating. |
Coats windings and insulation | Reduces heat dissipation and efficiency. |
Increases oil viscosity | Hinders proper oil circulation. |
✅ Sludge formation restricts cooling and accelerates component aging.
C. Acidity (Oil Oxidation and Acid Formation)
How it occurs:
- Oxidation reactions between oil and oxygen.
- Breakdown of hydrocarbon molecules in oil.
- Contamination from dissolved metals.
Effect | Consequence |
---|---|
Corrodes transformer components | Weakens metal parts and insulation. |
Increases oil conductivity | Lowers insulation effectiveness. |
Accelerates sludge formation | Causes cooling inefficiencies. |
✅ Acidic oil must be filtered or replaced to prevent corrosion and insulation damage.
D. Dissolved and Free Gas Contamination
How it occurs:
- Arcing and overheating decompose oil into gases.
- Partial discharges and corona discharges release gases.
- Poorly sealed systems allow air ingress.
Effect | Consequence |
---|---|
Reduces insulation strength | Increases risk of electrical breakdown. |
Indicates internal faults | Sign of overheating or arcing. |
Promotes bubble formation | Can lead to voltage breakdown. |
✅ Dissolved gas analysis (DGA) helps detect early faults before failure.
2. How Oil Contamination Affects Transformer Performance
A. Degraded Insulation Strength
- Low dielectric strength leads to insulation breakdown.
- Increases risk of electrical faults and short circuits.
- Moisture, acids, and gases reduce insulation reliability.
B. Reduced Cooling Efficiency
- Sludge and sediment block cooling ducts.
- Increased oil viscosity hinders heat dissipation.
- Overheating accelerates insulation aging.
C. Increased Internal Faults and Arcing
- Dissolved gases indicate arcing and partial discharges.
- Carbon deposits from decomposed oil create conductive paths.
- Leads to higher maintenance costs and transformer downtime.
D. Accelerated Transformer Aging
- Corrosion of metal parts weakens structural integrity.
- Oxidation and moisture cause premature failure.
- Unclean oil leads to frequent breakdowns and expensive repairs.
💡 Clean transformer oil ensures stable insulation, efficient cooling, and extended equipment life.
3. Key Transformer Oil Tests to Detect Contamination
Regular testing identifies oil contamination before transformer performance declines.
Test | Detects | Acceptable Limit |
---|---|---|
Dielectric Strength Test | Moisture, impurities | >30 kV |
Moisture Content Test | Water contamination | <10 ppm |
Acid Number (TAN Test) | Oil oxidation | <0.05 mg KOH/g |
Dissolved Gas Analysis (DGA) | Arcing, overheating | Gas-specific limits |
Interfacial Tension Test | Oil purity | >25 mN/m |
✅ Routine oil testing ensures contaminants are detected early, preventing major failures.
4. Preventive Maintenance to Reduce Oil Contamination
A. Filtration and Purification
When to perform:
- Moisture content exceeds 10 ppm.
- Dielectric strength drops below 25 kV.
- Oil shows signs of oxidation (increased acidity).
Filtration Method | Purpose | Frequency |
---|---|---|
Vacuum Filtration | Removes moisture and dissolved gases | Every 3-5 years |
Centrifugal Separation | Eliminates solid contaminants | As needed |
Oil Regeneration | Restores chemical properties | Every 5-7 years |
B. Oil Replacement
When to replace oil:
- Acid number (TAN) >0.2 mg KOH/g.
- Breakdown voltage below 20 kV.
- Excessive sludge formation and oxidation.
💡 Replacing severely degraded oil prevents long-term transformer damage.
C. Moisture Control and Sealing Maintenance
- Use silica gel breathers to absorb moisture.
- Regularly inspect and replace gaskets.
- Ensure proper sealing to prevent air ingress.
✅ Keeping moisture out prevents rapid oil degradation.
D. Cooling System Maintenance
- Flush radiators and cooling ducts to prevent sludge buildup.
- Ensure fans and oil pumps are functioning properly.
- Monitor top-oil and winding temperatures.
✅ Proper cooling extends insulation life and improves efficiency.
What Are the Best Practices for Transformer Oil Maintenance and Replacement?
Transformer oil is essential for insulation, cooling, and preventing internal faults in oil-immersed transformers. However, over time, contaminants such as moisture, sludge, and dissolved gases degrade the oil, reducing its effectiveness. Proper oil maintenance and timely replacement ensure transformer reliability, prevent failures, and extend operational life.
Best practices for transformer oil maintenance and replacement include routine oil testing, filtration to remove contaminants, moisture control, and scheduled oil changes. Regular monitoring of dielectric strength, acidity, and dissolved gas content helps detect early signs of oil degradation, preventing transformer insulation breakdown and overheating.
This guide outlines key maintenance procedures, oil testing methods, and best practices for keeping transformer oil in optimal condition.
Transformer oil does not require maintenance as long as the transformer is operational.False
Regular transformer oil maintenance is essential to remove contaminants, prevent insulation failure, and extend transformer life.
1. Why Transformer Oil Maintenance Is Essential
Transformer oil maintenance prevents:
✅ Insulation failure by removing moisture and impurities.
✅ Overheating by ensuring efficient heat dissipation.
✅ Corrosion and sludge formation, preserving transformer components.
✅ Costly breakdowns by detecting early signs of oil degradation.
💡 Well-maintained transformer oil extends transformer life by 30-50%.
2. Key Transformer Oil Tests for Maintenance
Regular oil testing helps determine whether filtration, purification, or replacement is necessary.
Test | Purpose | Acceptable Limit | Frequency |
---|---|---|---|
Dielectric Strength Test (BDV) | Ensures insulation capability | >30 kV | Every 6-12 months |
Dissolved Gas Analysis (DGA) | Detects arcing, overheating | Gas-specific limits | Yearly |
Moisture Content Test | Prevents insulation degradation | <10 ppm | Yearly |
Acidity (TAN Test) | Monitors oil oxidation | <0.05 mg KOH/g | Yearly |
Interfacial Tension Test | Identifies oil contamination | >25 mN/m | Yearly |
✅ Regular oil testing helps detect contamination before it causes transformer failure.
3. Best Practices for Transformer Oil Maintenance
A. Oil Filtration and Purification
Purpose: Removes moisture, gases, and solid contaminants to restore oil quality.
Filtration Method | Purpose | When to Perform |
---|---|---|
Vacuum Filtration | Removes moisture and dissolved gases | If moisture >10 ppm or BDV <25 kV |
Centrifugal Separation | Eliminates solid contaminants | If sludge or dirt is detected |
Micron Filtration (1-5 µm) | Captures fine particles | During routine maintenance |
Procedure:
- Heat transformer oil to 60-70°C to reduce viscosity.
- Pass oil through a vacuum filtration unit to remove water and gases.
- Filter oil through a fine micron filter to capture sludge and impurities.
- Test dielectric strength before returning oil to service.
✅ Filtration restores oil quality without needing a full replacement.
B. Moisture Control and Prevention
Purpose: Prevents moisture contamination, which lowers insulation strength.
Moisture Prevention Method | Action |
---|---|
Silica Gel Breathers | Replace when color changes from blue to pink. |
Sealed Transformer System | Inspect for leaks and replace faulty gaskets. |
Regular Oil Sampling | Detect moisture early and perform filtration if needed. |
✅ Moisture-free oil prevents insulation breakdown and dielectric failure.
C. Cooling System Maintenance
Purpose: Ensures transformer oil circulates properly to dissipate heat efficiently.
Component | Maintenance Action | Frequency |
---|---|---|
Radiators & Cooling Fans | Clean to remove dirt buildup | Every 6 months |
Oil Pumps & Circulators | Check for proper operation | Yearly |
Temperature Monitoring | Ensure oil stays within limits (<85°C) | Continuous |
✅ Proper cooling prevents overheating and extends transformer oil life.
4. When and How to Replace Transformer Oil
A. When to Replace Transformer Oil
Condition | Action Required |
---|---|
Breakdown voltage <20 kV | Replace oil immediately |
Acid number (TAN) >0.2 mg KOH/g | Replace oil |
Excessive sludge or oxidation detected | Replace or regenerate oil |
💡 Oil replacement should only be performed if filtration cannot restore quality.
B. Oil Replacement Procedure
- Drain the old transformer oil completely.
- Flush the transformer tank with new oil to remove residues.
- Refill the transformer with high-quality, filtered oil.
- Perform vacuum degassing to remove trapped air bubbles.
- Test oil dielectric strength before re-energizing.
✅ Proper oil replacement restores insulation and cooling efficiency.
5. Common Transformer Oil Issues and Solutions
Issue | Cause | Solution |
---|---|---|
Low Dielectric Strength | Moisture contamination | Perform oil filtration |
High Acidity (TAN Test Fail) | Oxidation and sludge formation | Replace oil |
Overheating | Poor cooling system performance | Check radiators and fans |
Dissolved Gases Detected | Arcing, overheating, or internal faults | Perform DGA and investigate faults |
✅ Preventive oil maintenance reduces breakdown risks and repair costs.
6. Best Practices for Long-Term Transformer Oil Care
- Test transformer oil regularly to detect contamination early.
- Perform filtration every 3-5 years to remove impurities.
- Replace silica gel breathers to keep moisture out.
- Maintain proper sealing to prevent oil oxidation.
- Monitor oil temperature and dielectric strength continuously.
💡 Proactive oil maintenance ensures transformers run efficiently for decades.
How Can You Extend the Lifespan of Transformer Oil and Improve Efficiency?
Transformer oil is essential for insulation, cooling, and fault protection in oil-immersed transformers. However, contamination, oxidation, and overheating gradually degrade the oil, reducing its effectiveness and increasing the risk of transformer failure. Proper oil maintenance can extend its lifespan, enhance efficiency, and reduce maintenance costs.
Extending the lifespan of transformer oil and improving efficiency involves regular oil testing, filtration, moisture control, oxidation prevention, and optimized cooling management. By maintaining clean oil with high dielectric strength, transformers operate more reliably, reducing downtime and energy losses.
This guide explains best practices for oil preservation, key maintenance strategies, and efficiency-boosting techniques for long-term transformer reliability.
Transformer oil does not degrade over time and does not require maintenance.False
Transformer oil degrades due to oxidation, contamination, and moisture absorption, requiring regular maintenance to maintain efficiency and prevent failures.
1. Why Transformer Oil Maintenance Matters
Proper transformer oil care ensures:
✅ Stronger insulation by maintaining high dielectric strength.
✅ Efficient heat dissipation, preventing overheating.
✅ Longer oil lifespan, reducing replacement costs.
✅ Lower energy losses, improving transformer performance.
💡 Neglecting oil maintenance can lead to premature transformer failure, costly repairs, and increased power losses.
2. Key Factors That Reduce Transformer Oil Lifespan
A. Moisture Contamination
- Lowers dielectric strength, increasing insulation failure risks.
- Speeds up oxidation, leading to acidity buildup.
B. Oxidation and Acidity Increase
- Forms sludge and deposits, reducing cooling efficiency.
- Corrodes transformer components, weakening internal parts.
C. Dissolved Gases from Overheating
- Indicates insulation breakdown or arcing.
- Reduces insulation effectiveness, increasing failure risk.
D. Particulate Contaminants
- Accelerates oil degradation and sludge formation.
- Blocks cooling pathways, increasing transformer temperature.
💡 Addressing these issues through regular maintenance improves oil efficiency and transformer performance.
3. Best Practices for Extending Transformer Oil Lifespan
A. Regular Transformer Oil Testing
Purpose: Detects contaminants, degradation, and insulation weakness before failure occurs.
Test | Purpose | Recommended Frequency | Acceptable Limit |
---|---|---|---|
Dielectric Strength (BDV) | Ensures insulation capability | Every 6-12 months | >30 kV |
Dissolved Gas Analysis (DGA) | Identifies arcing, overheating | Yearly | Gas-specific limits |
Moisture Content | Prevents insulation degradation | Yearly | <10 ppm |
Acidity (TAN Test) | Monitors oxidation levels | Yearly | <0.05 mg KOH/g |
Interfacial Tension (IFT) | Detects contamination | Yearly | >25 mN/m |
✅ Regular oil testing prevents unexpected breakdowns and extends transformer life.
B. Oil Filtration and Purification
Purpose: Removes moisture, gases, and solid contaminants to restore oil quality.
Filtration Method | Purpose | Frequency |
---|---|---|
Vacuum Filtration | Removes moisture and dissolved gases | Every 3-5 years |
Centrifugal Separation | Eliminates solid contaminants | As needed |
Micron Filtration (1-5 µm) | Captures fine particles | During routine maintenance |
✅ Filtration restores transformer oil quality without requiring full replacement.
C. Moisture Control and Prevention
Purpose: Prevents water contamination, preserving insulation strength.
Moisture Prevention Method | Action |
---|---|
Silica Gel Breathers | Replace when color changes from blue to pink. |
Sealed Transformer System | Inspect for leaks and replace faulty gaskets. |
Regular Oil Sampling | Detect moisture early and perform filtration if needed. |
✅ Dry oil prevents electrical breakdown and extends insulation life.
D. Cooling System Optimization
Purpose: Ensures efficient heat dissipation, preventing overheating.
Component | Maintenance Action | Frequency |
---|---|---|
Radiators & Cooling Fans | Clean to remove dirt buildup | Every 6 months |
Oil Pumps & Circulators | Check for proper operation | Yearly |
Temperature Monitoring | Ensure oil stays within safe limits (<85°C) | Continuous |
✅ Optimized cooling prevents oil degradation and improves efficiency.
4. When and How to Replace Transformer Oil
A. When to Replace Transformer Oil
Condition | Action Required |
---|---|
Breakdown voltage <20 kV | Replace oil immediately |
Acid number (TAN) >0.2 mg KOH/g | Replace oil |
Excessive sludge or oxidation detected | Replace or regenerate oil |
💡 Replace oil only if filtration cannot restore quality.
B. Oil Replacement Procedure
- Drain the old transformer oil completely.
- Flush the transformer tank with clean oil to remove residues.
- Refill the transformer with high-quality, filtered oil.
- Perform vacuum degassing to remove trapped air bubbles.
- Test oil dielectric strength before re-energizing.
✅ Proper oil replacement restores insulation and cooling efficiency.
5. Enhancing Transformer Efficiency Through Oil Maintenance
A. Preventing Energy Losses
- Clean oil maintains strong insulation, reducing electrical losses.
- Efficient heat dissipation lowers power consumption.
- Regular maintenance prevents forced shutdowns and downtime.
B. Reducing Operating Costs
- Extends oil lifespan, minimizing replacement costs.
- Prevents expensive transformer failures.
- Improves overall power efficiency, lowering energy bills.
💡 A well-maintained transformer runs at peak efficiency, reducing long-term operational costs.
6. Common Transformer Oil Issues and Solutions
Issue | Cause | Solution |
---|---|---|
Low Dielectric Strength | Moisture contamination | Perform oil filtration |
High Acidity (TAN Test Fail) | Oxidation and sludge formation | Replace oil |
Overheating | Poor cooling system performance | Clean radiators and fans |
Dissolved Gases Detected | Arcing, overheating, or internal faults | Perform DGA and investigate faults |
✅ Preventive maintenance reduces breakdown risks and repair costs.
7. Long-Term Best Practices for Transformer Oil Maintenance
- Perform regular oil testing to detect contamination early.
- Use high-quality transformer oil with strong oxidation resistance.
- Schedule filtration every 3-5 years to remove contaminants.
- Replace silica gel breathers to keep moisture out.
- Maintain proper sealing to prevent oxidation and sludge formation.
- Monitor oil temperature and dielectric strength continuously.
💡 Following these best practices ensures transformer oil remains clean, efficient, and long-lasting.
Conclusion
Transformer oil is a vital component of oil-immersed transformers, providing insulation, cooling, and protection against electrical faults. Understanding the different types of transformer oil, conducting regular testing, and following proper maintenance procedures are essential for ensuring long-term transformer reliability and efficiency.
By implementing proactive oil monitoring and maintenance, operators can prevent failures, reduce operational costs, and extend the lifespan of their transformers.
Need expert guidance on transformer oil selection, testing, or maintenance? Contact us today for professional solutions!
References
- Transformer Oil Types and Properties - https://www.electrical4u.com/transformer-oil/ - Electrical4U
- Transformer Oil Testing Methods - https://www.electronics-tutorials.ws/transformer/transformer-oil-testing.html - Electronics Tutorials
- Importance of Transformer Oil Maintenance - https://www.engineeringworld.com/transformer-oil-maintenance/ - Engineering World
- Dissolved Gas Analysis of Transformer Oil - https://www.sciencedirect.com/topics/engineering/dissolved-gas-analysis - ScienceDirect
- Transformer Oil Contaminants and Effects - https://www.transformers-magazine.com/technical-articles/transformer-oil-contaminants - Transformers Magazine
- Synthetic vs Mineral Transformer Oil - https://www.tdworld.com/transformers/article/20963964/synthetic-vs-mineral-oil-in-transformers - T&D World
- Transformer Oil Filtration Techniques - https://www.electricalengineeringportal.com/transformer-oil-filtration - Electrical Engineering Portal
- Guide to Transformer Oil Replacement - https://www.utilityproducts.com/transformer-maintenance/guide-transformer-oil-replacement - Utility Products
- IEEE Guide for Transformer Oil Testing - https://standards.ieee.org/standard/C57_104-2019.html - IEEE Standards
- Moisture Impact on Transformer Oil - https://www.power-grid.com/transformers/the-effect-of-moisture-on-transformer-oil/ - Power Grid